Titanium
Titanium is a chemical element with the symbol Ti and atomic number 22. Titanium was discovered in Cornwall, Great Britain, by William Gregor in 1791 and named by Martin Heinrich Klaproth for the Titans of Greek mythology. The two most useful properties of the metal form are corrosion resistance and the highest strength-to-weight ratio of any metal. In its unalloyed condition, titanium is as strong as some steels, but 45% lighter.
The alpha and beta forms of titanium
Pure titanium exists in two crystallographic forms. The first is alpha, which has a hexagonal close-packed crystal structure that is stable up to 1620º F (880º C). At that point, it transforms to a body-centered cubic structure, the beta phase, which is stable to the melting point.
As alloying elements are added to pure titanium, they tend to change the temperature at which the phase transformation occurs and the amount of each phase present. Alloy additions tend to stabilize either the alpha phase to higher temperatures or the beta phase to lower temperatures. The most important alpha stabilizers are aluminum and oxygen; the key beta stabilizers include molybdenum, vanadium, chromium and iron.
There are four basic classes of titanium-based materials – , , , and – each favoring selected, specific characteristics. The family of titanium alloys offers a full range of strength to the very high-strength. Most of the alpha-beta and beta alloys can provide a myriad of strength-ductility property combinations through adjustments in alloy heat treatment and/or composition. With the wide selection of titanium alloys available, optimum choice for a given environment is almost always possible.
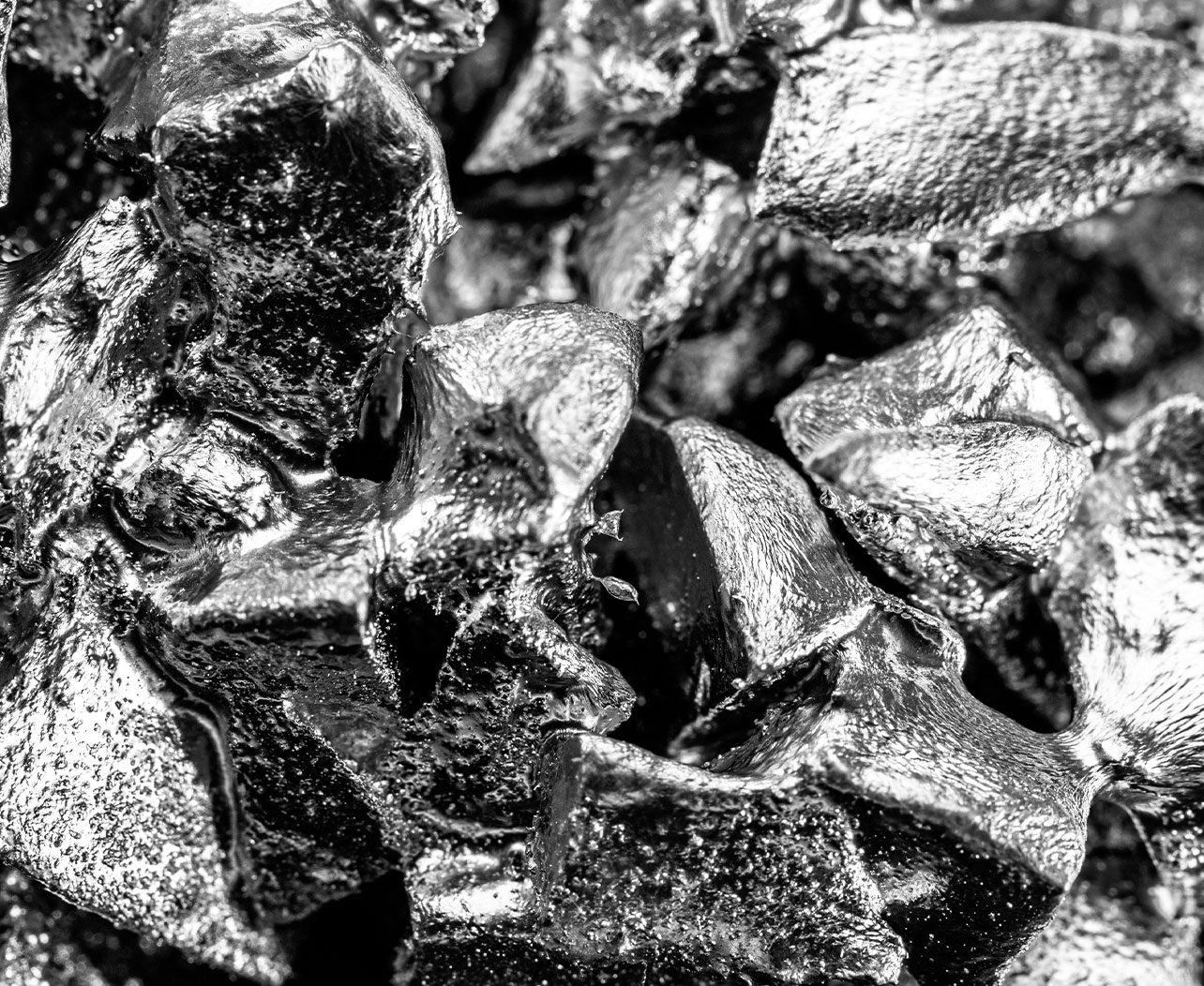
Common applications:
- Aerospace parts
- Missiles
- Oil and Gas parts
- Automotive parts
- Medical prostheses
- rthopedic implants
- Dental implants
- Sporting goods
- Jewelry
Hints for Machining Titanium
- Titanium with proper procedures can be fabricated using techniques no more difficult than are used machining Type 316 stainless steel.
- Commercially pure grades of Titanium with tensile strengths of 241 MPA to 550 MPA machine much easier than the aircraft alloys (i.e.) 6AL/4V with tensile strengths up to 1380 MPA.
- Titanium’s work hardening rate is less than that of austenetic stainless steel, about equivalent to 0.20 carbon steel.
- Titanium requires low shearing forces, demonstrates an absence of “built-up edge” and is not notch sensitive.
- Titanium if classified as difficult to machine, is due to its physical properties.
- Titanium is a poor conductor of heat. As a result heat caused by the cutting action does not dissipate quickly.
- Titanium has a strong alloying tendency or chemical reactivity with materials in the cutting tools which cause galling, welding, smearing, and rapid destruction of the cutting tool.
- Titanium due to its relatively low modulus will have a tendency to move away from the cutting tool unless heavy cuts are maintained or proper back-up is employed.
Two other factors influence machining operations:
- Because of the lack of a stationary mass of metal (built-up edge) ahead of the cutting tool, a high shearing angle is formed. This causes a thin chip to contact a relatively small area on the cutting tool face and results in high bearing loads per unit area. The high bearing force, combined with the friction developed by the chip as it rushes over the bearing area, results in a great increase in heat on a very localized portion of the cutting tool.
- Further, the combination of high bearing forces and heat produces cratering action close to the cutting edge, resulting in rapid tool breakdown.
The basic machining properties of Titanium cannot be altered; however the following basic rules have been developed in machining Titanium:
- Use low cutting speeds.
- Maintain high feed rates. Temperature is not affected by feed rate so much as by speed, and the highest feed rates consistent with good machining practice should be used.
- Use copious amounts of cutting fluid.
- Use sharp tools and replace them at first signs of wear. Tool failure occurs quickly after a small initial amount of wear.
- Never stop feeding while tool and work are in moving contact. Allowing a tool to dwell in moving contact causes work hardening and promotes smearing, galling, seizing and tool breakdown.
The following recommendations for speeds, feeds and other parameters presented in this brochure are recommendations and should be considered only as good starting points.
Data Sheets
The following specification data sheets are provided as PDF files. You must have Acrobat Reader to view and/or save these files. A free version of Acrobat Reader is available to download here.